By Haven McCall, DRSc, CEO, Canyon Labs02.14.23
In 2023, since the COVID-19 pandemic, there has clearly been an increased level of consumer interest in health and wellness products. New dietary supplement brands are entering the natural products marketplace to meet the newly increased consumer demand. How can these brands keep up with demand in a responsible way that ensures safety requirements are maintained?
Many dietary supplement brands entering the natural products industry lack the financial resources and the technical expertise to manufacture in-house.1 Enter contract manufacturers. Did you know a high volume of dietary supplements sold in the U.S. are manufactured by contract manufacturers? Some estimates anticipate that the global dietary supplement contract manufacturing category will grow from $7.4 billion to $11.5 billion by 2028.2
For many brands, their contract partners are the lifeblood of their innovation. But as always, with great power comes great responsibility. For brand and contract manufacturers, one key requirement includes manufacturing products according to the U.S. Food and Drug Administration’s (FDA) current good manufacturing practices (cGMPs).
The dietary supplement (DS) cGMP rule in 21 CFR part 111 (“the DS cGMP rule”) requires persons who manufacture, package, label, or hold a dietary supplement to establish and follow current good manufacturing practices, to ensure the quality of the dietary supplement, and to ensure that the dietary supplement is packaged and labeled as specified in the master manufacturing record.
This ruling established minimum regulations necessary to ensure that activities related to manufacturing, packaging, or holding dietary ingredients or dietary supplements are done in a manner that will not adulterate or misbrand such nutritional ingredients or dietary supplements.
While the ultimate responsibility lies with the brand owner to make sure each party within the supply chain is compliant according to cGMPs, the regulation applies to every single manufacturer within the supply chain, including raw material suppliers, contract manufacturers, and the final manufacturer whose name is on the bottle.
Recent warning letters and lawsuits have also highlighted that the buck doesn’t stop with the final manufacturer. Retailers are also facing the consequences of not verifying the quality of the products they carry.4 Failure to comply with cGMPs can result in warning letters by the FDA and the classification of a brand/product as adulterated.
While cGMP regulations have been around for 15 years, 483 form observations and warning letters are consistently issued. In fact, FDA issues an average of 1,600 observations and 25 warning letters per year.5-7 Many observations and warning letters cite cGMP violations as the primary cause.
After product testing of the Life Rising DHZC-2 tablets, the FDA found elevated lead levels (56 times higher than safe levels). Subsequently, the FDA learned of another child with elevated lead levels and two more reported deaths of people who took the supplement, resulting in a decision to cease distribution of all Life Rising products and a recall to remove the unsafe products from the market.
Because of the significant identified risk to consumer health and safety, the FDA inspected the Life Rising manufacturing facility. During the inspection, the investigator found numerous cGMP violations identified within 21 CFR Part 111.8
These violations found that products were manufactured, packed, and held under unsanitary conditions. The investigation also revealed that no quality system or production and process controls had been implemented. Furthermore, no identity, purity, strength, and composition specifications were established for each finished batch of the product, and no testing was performed on the finished product to determine if those specifications were met.
Additionally, the investigator noted that manufacturing and batch records could not be found for any of the products manufactured at the facility.
Had a quality program been implemented within this organization, most of, if not all, the violations could have been prevented. While this can be viewed as an extreme example or a case of “one bad apple,” 1,600 yearly observations point to a more systemic issue yet to be addressed.
This is no easy task, especially for new brand manufacturers entering the U.S. health and wellness marketplace. As a recently established brand, they are often already wearing multiple hats and overwhelmed with the ins and outs of a business. As a 23-year expert in regulatory and quality affairs, here are a few recommendations to consider while developing and implementing a quality program:
1. First and foremost, identify quality and regulatory experts who can work with you and your contract manufacturer to develop a quality strategy and system for your brand(s).
Then identify/establish specifications for your product as well as the process of testing. Record all of it in an official Standard Operating Procedure (SOP).
2. Remember to audit the raw material supplier. A quality dietary supplement starts with quality ingredients. Therefore, it is critical to have a comprehensive understanding of your supply chain. Make sure that you or your contract manufacturer is conducting identity testing for every lot of raw material going into the finished product formulation. Testing the incoming raw material can save companies a lot of headaches down the supply chain before it gets to a point where it costs the company millions of dollars or is too late in the process to backtrack. So do it right the first time, from the beginning, by testing the raw materials.
3. Once the raw material is verified, work with the contract manufacturer and/or third-party experts to establish testing protocols and a monitoring schedule for your finished batch. An essential third-party resource to get involved early on could be an ISO 17025 accredited lab that you or your contract manufacturer selects. When choosing an ISO 17025-accredited lab, look for one with manufacturing expertise and experience in setting up quality programs.
4. Make sure your testing protocols include the “Big Five.”9 This includes identity, purity, strength, composition, and potential contamination testing. Add one more: stability testing. Performing real-time and accelerated stability will help identify your products’ shelf-life and routinely monitor any changes.
5. In any given year, FDA usually conducts 500-600 inspections. In FY22, FDA conducted close to 500 inspections.10 Reviewing the inspection observations as per 21 CFR 111, FDA has issued more than 40 observations for not using scientifically valid methods or appropriate tests.5 Therefore, working with a third-party laboratory or experts who can help identify and develop appropriate tests for your product is critical.
6. No matter the level of due diligence, there are bound to be quality-related hiccups in the manufacturing process. The more critical question is what procedures are in place to address those hiccups. It is essential to have a quality unit group that can oversee and make the hard decisions related to product release, reject raw materials and finished batches due to out-of-specification (OOS) testing results, and potentially review any manufacturing deviations.
From raw material suppliers to contract manufacturers to retailers, and everyone in between, ensuring quality must be a collective responsibility. The long-term success of our industry depends on all of us upholding this obligation each step of the way.
About the Author: Dr. Haven McCall currently serves as the CEO at Canyon Labs. He has spent the last 23 years working in key positions at large, multinational corporations in the areas of clinical research, quality, and regulatory. His doctoral studies at the University of Southern California focused on improving the standard of care for patients through risk mitigation and quality principles. McCall is an active member of the Collaborative Institutional Training Initiative (CITI Program), Society of Clinical Research Associates (SOCRA), Regulatory Affairs Professionals Society (RAPS), American Society for Quality (ASQ), Project Management Institute (PMI), and The Organization for Professionals in Regulatory Affairs (TOPRA - Europe). He has participated within these organizations to drive improvements for industry best practices, regulations, guidance documents, accreditation standards, and European directives. In addition to his CEO role, McCall currently teaches graduate-level courses in clinical research, quality, and regulatory practices at Johns Hopkins University.
2. Business Research Insights. (2023). Dietary Supplement Contract Manufacturing Market Size, Global Report, 2021 – 2028. https://www.businessresearchinsights.com/market-reports/dietary-supplement-contract-manufacturing-market-102792. Published January 2023. Accessed February 10, 2023.
3. Federal Register. (2003). Current Good Manufacturing Practice in Manufacturing, Packing, or Holding Dietary Ingredients and Dietary Supplements. https://www.federalregister.gov/documents/2003/03/13/03-5401/current-good-manufacturing-practice-in-manufacturing-packing-or-holding-dietary-ingredients-and. Published March 2003. Accessed February 10, 2023.
4. U.S. Food and Drug Administration. (2020). FDA In Brief: FDA Issues Warning Letter to Whole Foods Market After Repeated Recalls of Foods Packaged with Incorrect Allergen Labeling. https://www.fda.gov/news-events/fda-brief/fda-brief-fda-issues-warning-letter-whole-foods-market-after-repeated-recalls-foods-packaged. Published December 2020. Accessed February 10, 2023.
5. U.S. Food and Drug Administration. (2022). Inspection Observations https://www.fda.gov/inspections-compliance-enforcement-and-criminal-investigations/inspection-references/inspection-observations. Published November 2022. Accessed February 10, 2023.
6. U.S. Food and Drug Administration. (2023). Warning Letters. https://www.fda.gov/inspections-compliance-enforcement-and-criminal-investigations/compliance-actions-and-activities/warning-letters. Published February 2023. Accessed February 10, 2023.
7. Regulatory Focus, A Raps Publication. (2021). Current status and future FDA enforcement of dietary supplements. https://www.raps.org/news-and-articles/news-articles/2021/6/current-status-and-future-fda-enforcement-of-dieta. Published June 2021. Accessed February 10, 2023.
8. U.S. Food and Drug Administration. (2017). Warning Letter: Life Rising Corporation https://www.fda.gov/inspections-compliance-enforcement-and-criminal-investigations/warning-letters/life-rising-corporation-516209-05252017. Published June 2017. Accessed February 10, 2023.
9. Natural Products Insider. (2022). Contract manufacturing: Cooperation, compliance, COVID recovery, and more. Published April 2022. Accessed February 10, 2023.
10. Natural Products Insider. (2022). FDA audits climb in FY22 for dietary supplement facilities. https://www.naturalproductsinsider.com/regulatory/fda-audits-climb-fy22-dietary-supplement-facilities. Published October 2022. Accessed February 10, 2023.
Many dietary supplement brands entering the natural products industry lack the financial resources and the technical expertise to manufacture in-house.1 Enter contract manufacturers. Did you know a high volume of dietary supplements sold in the U.S. are manufactured by contract manufacturers? Some estimates anticipate that the global dietary supplement contract manufacturing category will grow from $7.4 billion to $11.5 billion by 2028.2
For many brands, their contract partners are the lifeblood of their innovation. But as always, with great power comes great responsibility. For brand and contract manufacturers, one key requirement includes manufacturing products according to the U.S. Food and Drug Administration’s (FDA) current good manufacturing practices (cGMPs).
What Are cGMPs, and Why Are They Important?
In 2007, the FDA published a final rule that established a regulation (21 CFR Part 111) for cGMPs that apply to manufacturing, packaging, labeling, or holding operations of dietary supplements.3The dietary supplement (DS) cGMP rule in 21 CFR part 111 (“the DS cGMP rule”) requires persons who manufacture, package, label, or hold a dietary supplement to establish and follow current good manufacturing practices, to ensure the quality of the dietary supplement, and to ensure that the dietary supplement is packaged and labeled as specified in the master manufacturing record.
This ruling established minimum regulations necessary to ensure that activities related to manufacturing, packaging, or holding dietary ingredients or dietary supplements are done in a manner that will not adulterate or misbrand such nutritional ingredients or dietary supplements.
While the ultimate responsibility lies with the brand owner to make sure each party within the supply chain is compliant according to cGMPs, the regulation applies to every single manufacturer within the supply chain, including raw material suppliers, contract manufacturers, and the final manufacturer whose name is on the bottle.
Recent warning letters and lawsuits have also highlighted that the buck doesn’t stop with the final manufacturer. Retailers are also facing the consequences of not verifying the quality of the products they carry.4 Failure to comply with cGMPs can result in warning letters by the FDA and the classification of a brand/product as adulterated.
While cGMP regulations have been around for 15 years, 483 form observations and warning letters are consistently issued. In fact, FDA issues an average of 1,600 observations and 25 warning letters per year.5-7 Many observations and warning letters cite cGMP violations as the primary cause.
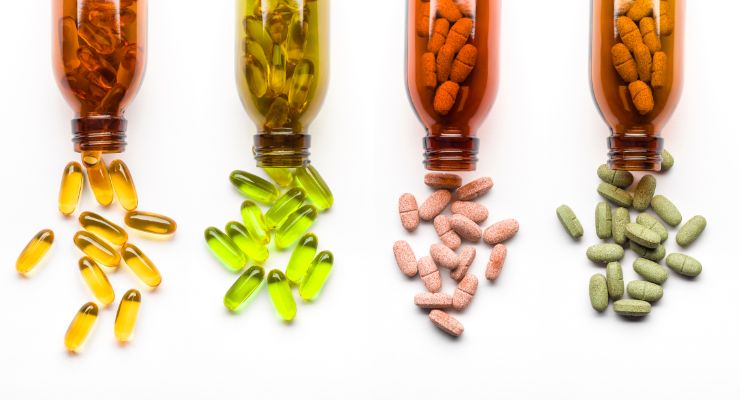
Adulterated Dietary Supplements
Use of illegal ingredients, disease claims, high levels of heavy metals, unsanitary manufacturing conditions, and mislabeling can all constitute cGMP violations. One prominent example of this took place in April of 2016. The Cook County Department of Health (Illinois) notified the FDA of a child with elevated lead levels who may have consumed a dietary supplement manufactured by Ton Shen Health.After product testing of the Life Rising DHZC-2 tablets, the FDA found elevated lead levels (56 times higher than safe levels). Subsequently, the FDA learned of another child with elevated lead levels and two more reported deaths of people who took the supplement, resulting in a decision to cease distribution of all Life Rising products and a recall to remove the unsafe products from the market.
Because of the significant identified risk to consumer health and safety, the FDA inspected the Life Rising manufacturing facility. During the inspection, the investigator found numerous cGMP violations identified within 21 CFR Part 111.8
These violations found that products were manufactured, packed, and held under unsanitary conditions. The investigation also revealed that no quality system or production and process controls had been implemented. Furthermore, no identity, purity, strength, and composition specifications were established for each finished batch of the product, and no testing was performed on the finished product to determine if those specifications were met.
Additionally, the investigator noted that manufacturing and batch records could not be found for any of the products manufactured at the facility.
Had a quality program been implemented within this organization, most of, if not all, the violations could have been prevented. While this can be viewed as an extreme example or a case of “one bad apple,” 1,600 yearly observations point to a more systemic issue yet to be addressed.
How to Avoid Becoming the ‘Poster Child’ for Violations
So, what can you do to avoid cGMP violations, whether using a contract manufacturer or manufacturing your own product? A critical step you should take is to implement a quality program that is compliant with FDA regulations and requirements.This is no easy task, especially for new brand manufacturers entering the U.S. health and wellness marketplace. As a recently established brand, they are often already wearing multiple hats and overwhelmed with the ins and outs of a business. As a 23-year expert in regulatory and quality affairs, here are a few recommendations to consider while developing and implementing a quality program:
1. First and foremost, identify quality and regulatory experts who can work with you and your contract manufacturer to develop a quality strategy and system for your brand(s).
Then identify/establish specifications for your product as well as the process of testing. Record all of it in an official Standard Operating Procedure (SOP).
2. Remember to audit the raw material supplier. A quality dietary supplement starts with quality ingredients. Therefore, it is critical to have a comprehensive understanding of your supply chain. Make sure that you or your contract manufacturer is conducting identity testing for every lot of raw material going into the finished product formulation. Testing the incoming raw material can save companies a lot of headaches down the supply chain before it gets to a point where it costs the company millions of dollars or is too late in the process to backtrack. So do it right the first time, from the beginning, by testing the raw materials.
3. Once the raw material is verified, work with the contract manufacturer and/or third-party experts to establish testing protocols and a monitoring schedule for your finished batch. An essential third-party resource to get involved early on could be an ISO 17025 accredited lab that you or your contract manufacturer selects. When choosing an ISO 17025-accredited lab, look for one with manufacturing expertise and experience in setting up quality programs.
4. Make sure your testing protocols include the “Big Five.”9 This includes identity, purity, strength, composition, and potential contamination testing. Add one more: stability testing. Performing real-time and accelerated stability will help identify your products’ shelf-life and routinely monitor any changes.
5. In any given year, FDA usually conducts 500-600 inspections. In FY22, FDA conducted close to 500 inspections.10 Reviewing the inspection observations as per 21 CFR 111, FDA has issued more than 40 observations for not using scientifically valid methods or appropriate tests.5 Therefore, working with a third-party laboratory or experts who can help identify and develop appropriate tests for your product is critical.
6. No matter the level of due diligence, there are bound to be quality-related hiccups in the manufacturing process. The more critical question is what procedures are in place to address those hiccups. It is essential to have a quality unit group that can oversee and make the hard decisions related to product release, reject raw materials and finished batches due to out-of-specification (OOS) testing results, and potentially review any manufacturing deviations.
Quality is Everyone’s Responsibility
At the end of the day, the objective of the dietary supplement cGMP rule in 21 CFR part 111 is to promote and protect public health. As promoters of good health, that is a goal we, the natural products industry, can all get behind.From raw material suppliers to contract manufacturers to retailers, and everyone in between, ensuring quality must be a collective responsibility. The long-term success of our industry depends on all of us upholding this obligation each step of the way.
About the Author: Dr. Haven McCall currently serves as the CEO at Canyon Labs. He has spent the last 23 years working in key positions at large, multinational corporations in the areas of clinical research, quality, and regulatory. His doctoral studies at the University of Southern California focused on improving the standard of care for patients through risk mitigation and quality principles. McCall is an active member of the Collaborative Institutional Training Initiative (CITI Program), Society of Clinical Research Associates (SOCRA), Regulatory Affairs Professionals Society (RAPS), American Society for Quality (ASQ), Project Management Institute (PMI), and The Organization for Professionals in Regulatory Affairs (TOPRA - Europe). He has participated within these organizations to drive improvements for industry best practices, regulations, guidance documents, accreditation standards, and European directives. In addition to his CEO role, McCall currently teaches graduate-level courses in clinical research, quality, and regulatory practices at Johns Hopkins University.
References
1. Nutraceuticals World. (2022). 2022 Contract Manufacturing Survey: Nutraceuticals and Pharmaceuticals. https://www.nutraceuticalsworld.com/issues/2022-03/view_features/2022-contract-manufacturing-survey. Published March 2022. Accessed February 10, 2023.2. Business Research Insights. (2023). Dietary Supplement Contract Manufacturing Market Size, Global Report, 2021 – 2028. https://www.businessresearchinsights.com/market-reports/dietary-supplement-contract-manufacturing-market-102792. Published January 2023. Accessed February 10, 2023.
3. Federal Register. (2003). Current Good Manufacturing Practice in Manufacturing, Packing, or Holding Dietary Ingredients and Dietary Supplements. https://www.federalregister.gov/documents/2003/03/13/03-5401/current-good-manufacturing-practice-in-manufacturing-packing-or-holding-dietary-ingredients-and. Published March 2003. Accessed February 10, 2023.
4. U.S. Food and Drug Administration. (2020). FDA In Brief: FDA Issues Warning Letter to Whole Foods Market After Repeated Recalls of Foods Packaged with Incorrect Allergen Labeling. https://www.fda.gov/news-events/fda-brief/fda-brief-fda-issues-warning-letter-whole-foods-market-after-repeated-recalls-foods-packaged. Published December 2020. Accessed February 10, 2023.
5. U.S. Food and Drug Administration. (2022). Inspection Observations https://www.fda.gov/inspections-compliance-enforcement-and-criminal-investigations/inspection-references/inspection-observations. Published November 2022. Accessed February 10, 2023.
6. U.S. Food and Drug Administration. (2023). Warning Letters. https://www.fda.gov/inspections-compliance-enforcement-and-criminal-investigations/compliance-actions-and-activities/warning-letters. Published February 2023. Accessed February 10, 2023.
7. Regulatory Focus, A Raps Publication. (2021). Current status and future FDA enforcement of dietary supplements. https://www.raps.org/news-and-articles/news-articles/2021/6/current-status-and-future-fda-enforcement-of-dieta. Published June 2021. Accessed February 10, 2023.
8. U.S. Food and Drug Administration. (2017). Warning Letter: Life Rising Corporation https://www.fda.gov/inspections-compliance-enforcement-and-criminal-investigations/warning-letters/life-rising-corporation-516209-05252017. Published June 2017. Accessed February 10, 2023.
9. Natural Products Insider. (2022). Contract manufacturing: Cooperation, compliance, COVID recovery, and more. Published April 2022. Accessed February 10, 2023.
10. Natural Products Insider. (2022). FDA audits climb in FY22 for dietary supplement facilities. https://www.naturalproductsinsider.com/regulatory/fda-audits-climb-fy22-dietary-supplement-facilities. Published October 2022. Accessed February 10, 2023.