Features
Nutraceutical Manufacturing Challenges and Certification Standards
Quality and product validation remain central to supplement industry despite series of challenges.
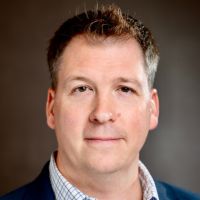
By: Sean Moloughney
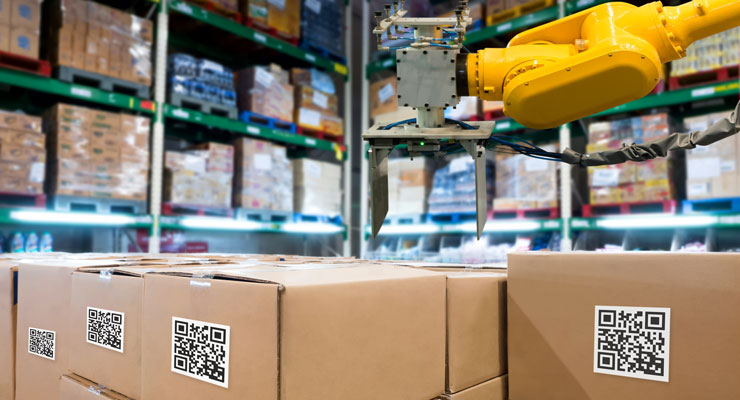
Faced with inflation, raw material shortages, shipping delays, a dwindling pool of workers, and more fallout two years into the COVID-19 pandemic, people, brands, and companies have faced challenges at every turn. Still, in the manufacturing business, quality cannot be compromised.
According to Scott Steinford, CEO of Health Wright Products, navigating modern supply chain issues requires several fundamental tools: communication, cooperation, and collaboration. “Now, more than ever, forecasts, supply contracts, and blanket orders are critical. Transparency from customers is important to establish accurate forecasts and lead times. The lengthy lead times for ingredients and components require advanced order planning from all stakeholders of the supply chain. Customers that have built relations with their vendors through loyalty and volume are experiencing benefits from the long term strategy of relationship building versus a more short term price/commodity mentality.”
Tough Terrain
The reality today is that common ingredients and components are still in short supply. For example, Steinford noted shortages of lid liners, foils and adhesives; corrugate; amino acids; alpha lipoic acid; minerals; and HPMC capsules.
“Packaging componentry is the worst category of the above mentioned with many lead times approaching or surpassing the one year mark,” he added. “Paper and plastic continue to be a pinch point for availability. Customers have had to be flexible in accepting changes to standard colors and components as opposed to some special order requirements that do not meet increasing minimum order levels.”
Flexibility, and an ability to pivot when needed, can lead to payoffs at times. Steinford noted success at Health Wright Products, which specializes in probiotic encapsulation, for generating awareness of the blister package format over plastic bottles. Enhancing probiotic protection, and offering a premium presentation, blister packaging has not experienced the lengthy lead time issues of plastic bottles and lids, he said.
Labor Shortage
On a fundamental level, today’s labor market, and what some have termed the “Great Resignation,” has affected production in a profound way that requires a fresh perspective.
“The key to retention rests in pay, culture, and flexibility,” said Steinford. “Recent Bureau of Labor Statistics reports manufacturing has been most affected by resignations with 60% turnover in late 2021 versus pre-pandemic measurements.”
Nearly all manufacturers have reported a need to be more competitive when it comes to wages, he added. “Wage increases have occurred but research has proven most people do not elect to change employment solely based on wages. Workers need respect, safe conditions, and flexibility. Employers must be attuned to the morale of the organization and respond to concerns quickly and with compassion.”
Overall, manufacturers face challenges from all directions, requiring adaptability and vision. “Quality, service, and value are the keystone ideals we implement to our customers and employees,” said Steinford. “While we can strive to provide these important attributes of our success, today’s pandemic-impacted environment continues to provide challenges in all aspects of production from ingredient to shipment. Raw material and worker shortages, price increases, wage increases, logistic complications, and more all factor into a challenging atmosphere for all aspects of our business. The adage ‘tough times never last, but tough people do’ is the mantra for our times.”
Certification Standards
Dietary supplement production was labeled as “essential” work during the pandemic by the U.S. government and was able to continue manufacturing products that consumers were stockpiling in the name of health and wellness.
Maintaining compliance with quality standards and good manufacturing practices didn’t stop either. Nor did the work of inspections and certifications from organizations like NSF International, which was able to adapt to new health and safety protocols and various local regulations, according to Edward Murray, senior manager of global health sciences certification, NSF International.
“This meant pivoting to virtual audits when necessary and possible, which we were fortunate enough to develop and implement rather quickly,” he said.
Ultimately, the best way to ensure consistent product quality “is to establish comprehensive quality agreements with any and all contract manufacturers,” Murray added. “These should include both facility inspections and testing protocols. The brands with the most rigorous safety measures also use GMP-certified facilities and seek third-party testing and certification for their products.”
Confronting a rash of e-commerce only products with questionable quality, Amazon recently updated requirements for selling supplements on its platform.
“NSF’s mission has always been to protect and improve human health,” said Murray. “It is encouraging that retailers and brands are working together to create new retail requirements aimed at better protecting consumers and allowing quality products to more effectively differentiate themselves in the market.”
Third-party validation and certification remains a differentiating factor in today’s competitive marketplace. “One of the best ways to offer confidence to brands, retailers, and consumers about product quality is by seeking and earning a certification from a trusted third-party,” Murray added. “Labels that bear NSF’s Contents Certified or Certified for Sport marks, for example, give assurance that the product was manufactured in a GMP-certified facility, it does not contain dangerous contaminants, and the facts panel and ingredient lists are accurate.”